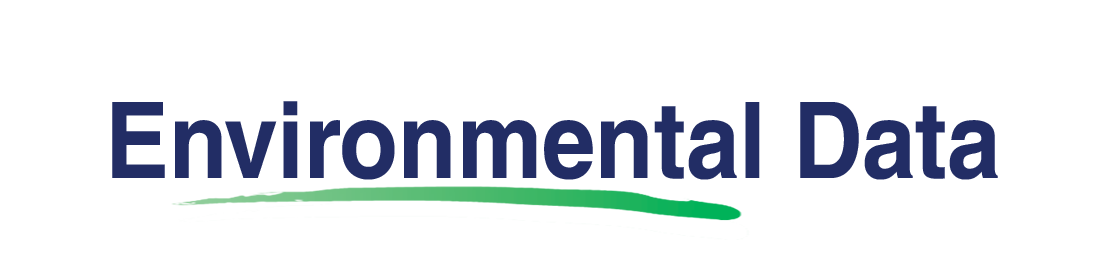
At PFB Corporation, we are concerned with the future of the planet and the effects that modern lifestyles may be having on climate change. PFB Corporation is committed to conducting its operations responsibly, mindful of the economic, environmental and social impacts of its operations.
PFB reports the material impacts our activity has on the environment. We tabulate and report our emissions, energy usage and waste generated. In 2013 PFB established a Sustainability Committee with members from all areas and specialties within our company.
The Committee’s mandate is to work with our management group and employees to facilitate continuous improvement of our sustainability performance. Our focus continues to be on improving our performance through a process of continuous improvement.
Green House Gas (GHG) – greenhouse gases are those gases which contribute to global warming. According to the Kyoto protocol significant greenhouse gases, emitted by human activity, include carbon dioxide (CO2), methane (CH4), nitrous oxide (N2O), hydrofluorocarbons (HFCs), perfluorocarbons (PFCs), and sulphur hexafluoride (SF6).
Ozone Depleting Substance (ODS) – A chemical compound that reaches the stratosphere and is capable of reacting with stratospheric ozone causing it to be depleted. Stratospheric ozone protects the earth from harmful UV radiation. PFB does not emit harmful ozone depleting substances from our manufacturing processes.
Volatile Organic Compounds (VOC) – any organic compound that can become vaporized under normal atmospheric conditions. VOC can contribute to the creation of ground level smog around urban centers. PFB releases VOC’s as part of our foam insulation production processes and we are sensitive to this issue and are actively working towards reductions in the amount of VOC’s we emit.
Waste is a significant issue for manufacturers like PFB both from a cost perspective and its environmental impact. PFB is continually looking for ways to reduce the generation of waste and, wherever possible, reuse and recycle. In 2022 we experienced a significant increase in waste to landfills over the previous year. The cause of this increase was due to an increase in production in some divisions. In 2023 PFB was able to improve its waste management process resulting in a decreased waste to landfill quantities (expressed as a percentage of outputs).
Both direct electricity usage and natural gas consumption was relatively unchanged in 2023 (<5% change). Energy consumption has been a significant focus of our individual facilities as we work toward improving efficiencies through installation of energy efficient lighting, equipment and implementing administrative controls for managing equipment operation schedules.
The energy savings potential from using PFB’s insulating products over the expected lifetime of those products (assumed to be 50 years) exceeds the amount of energy consumed in the manufacturing process by a ratio of approximately 120:1
(1) Estimated energy savings due to the installation of PFB foam insulation products per unit mass. Estimates based on data in “Energy and Greenhouse Gas Savings for EPS Foam Insulation Applied to Exterior Walls of Single Family Residential Housing In the U.S. and Canada”, Franklin Associates Ltd. February 2009. Energy savings based on reduction in heating when insulation installed as per assumptions in the Franklin report. Note that other insulation materials will provide equivalent reduction in energy and GHG savings if installed to the same level of thermal performance.
(2) Production energy includes embodied energy in raw materials as per “Energy and Environmental Profile of the US Chemical Industry” (May 2000 by Energetics Inc. for US Department of Energy) and direct production energy to manufacture in process raw materials and finished products.
We measure and monitor the total amount of electricity and natural gas consumed by our operations. Electricity and natural gas usage decreased slightly in 2023 over the previous year The decrease is not considered significant and likely due to small fluctuations in production quantities.
Electrical Notes - Electricity (green bars) refer to the left vertical axis, natural gas consumption (blue bars) refer to the right vertical axis. Fuel Used for Manufacturing refers to Natural gas and biomass to create steam for production process and heat for general building heat and process heat.
Water consumption decreased slightly in 2023 over the previous year due in part with water reduction strategies and fluctuating production rates. The rate of water use per material output went down slightly for a third year in a row due to gains in water usage efficiencies.
Over the past 10 years, PFB has completed several capital and research projects to substitute raw material inputs with materials that contain less VOC expanding agent. By substituting the raw materials PFB has made significant improvements in our VOC emissions intensity over the past several years.
The key emissions that we track are GHG’s, VOCs, NOx and SOx. We monitor emissions as a ratio of tonnes emitted to tonnes of EPS foam produced. Reductions in the ratios indicate better performance.
Since 2008 we reduced VOC emissions intensity due to efforts to introduce raw materials with lower VOC content. PFB’s long term plan is to continue converting applications and manufacturing facilities over to the lower VOC raw materials to continuously improve our impact on the environment. For example, in 2008, 13% of our raw materials consumed contained reduced levels of VOCs. In 2023 the usage of low VOC alternative raw material was >75% of the total resin input. This effort has resulted in an average VOC emissions avoidance of over 100 tonnes annually and a total reduction of 1000 tonnes over the past 10 years (avoided emissions - compared to emissions from using higher VOC raw materials).
Carbon dioxide, the principal greenhouse gas (GHG) emitted from PFB operations, arises from burning natural gas and other fuels in our production operations. We calculate and report GHG emissions in metric tonnes CO2 equivalents. Total direct GHG emissions and emissions intensity from PFB operations in 2023 was relatively unchanged over the previous year.
Our insulating products provide customers with the means to reduce their energy consumption and, consequently, their GHG emissions. The estimated GHG reductions that could be achieved if EPS insulation products made by PFB in 2023 were applied to exterior walls of single family residential houses in Canada is estimated to be approximately 50,000 metric tonne annually (a ratio of 5 to 1). Through improvements in the energy-efficiency of our processes we continue to focus on reducing our GHG emissions to further improve the net benefits provided by our products.
(1) Estimated GHG emissions reductions potential due to the installation of PFB foam insulation products sold during the reporting year - estimates based on data in “Energy and Greenhouse Gas Savings for EPS Foam Insulation Applied to Exterior Walls of Single Family Residential Housing In The U.S. and Canada”, Franklin Associates Ltd. February 2009. GHG savings is based on reduction in heating when insulation installed as per assumptions in the Franklin report. Note that other insulation materials will provide equivalent reduction in energy and GHG savings if installed to the same level of thermal performance.